
Creating the perfect pair of men’s cotton boat socks is no small feat. It involves countless hours of meticulous planning and collaboration among a talented team of designers, craftsmen, and technicians. Our commitment to quality, comfort, and style drives every step of our process, from initial concept to finished product.
The Vision and Design Process
Every great product begins with a vision. For our new range of men's cotton boat socks, we envisioned an ideal blend of comfort, durability, and contemporary fashion. To bring this vision to life, our team collaborated closely with both designers and footwear experts. This collaborative effort helped in conceptualizing the unique requirements that an ideal boat sock should meet - be it fit, breathability, or style. The journey started with numerous brainstorming sessions that led to initial sketches and prototypes. These early models served as tangible representations of our ideas, allowing us to refine the details before moving forward.
Selecting the Perfect Cotton
The backbone of any great sock is its fabric. We placed significant importance on selecting high-quality cotton that's not only soft but also durable. Ensuring ethical and sustainable sourcing was non-negotiable for us. We scoured suppliers who could provide ethically grown cotton to align with our environmental values. Before finalizing our choice, each cotton sample underwent rigorous testing to evaluate its softness and strength. Ultimately, this careful selection ensures that our customers enjoy unmatched comfort combined with long-lasting wear.
The Knitting Process
Once we had our premium cotton, the focus shifted to the knitting process. Utilizing advanced knitting techniques, we achieved seamless construction which prevents unnecessary friction against the skin. Consistency in quality and fit is paramount; hence specialized machinery played a crucial role in production. Each equipment piece is fine-tuned to maintain precision, ensuring that every pair of socks meets our stringent standards.
Dyeing and Color Selection
Aesthetics matter just as much as functionality. In choosing dyes, eco-friendliness was at the forefront of our decision-making process. We opted for ecologically responsible dyes that offer vibrant colors without harming the environment. Creating a palette that resonates with men’s fashion trends required extensive research and creativity. Moreover, these colors were tested rigorously to ensure they remain vivid and do not fade easily, guaranteeing longevity even after multiple washes.
Quality Control and Testing
No stone is left unturned when it comes to quality control. Rigorous wear and tear tests simulate real-world conditions to assess durability. Additionally, ensuring the perfect fit for different foot sizes requires exhaustive trial phases. We incorporated customer feedback obtained through various channels into our improvement loop, always striving to enhance user satisfaction based on actual experiences.
The Final Touches
To elevate the utility of our boat socks, additional features were considered essential. Anti-slip elements were added to prevent slipperiness, particularly beneficial for those active on boats or involved in sports. High-stress areas such as heels and toes were reinforced for added durability. Finally, branding and packaging received special attention to make sure that opening a pack of our socks feels like a premium experience.
Behind Every Pair: The Skilled Workforce
Our products are only as good as the hands that craft them. Meet the artisans and technicians whose expertise transforms raw materials into finely crafted boat socks. We uphold fair labor practices, ensuring that everyone involved receives their due compensation in safe working conditions. Continuous training programs keep our workforce skilled and motivated, supporting their growth parallel to our brand's evolution.
From Factory to Footwear Aisle
The journey doesn't end once the socks leave the factory floor. Efficient packing and shipping processes are implemented to minimize our carbon footprint while ensuring timely deliveries. Each package is meticulously inspected to confirm that it reaches customers in immaculate condition.
Customer Experience and Reviews
The final touchpoint in our product lifecycle is arguably the most important - the customer's first impression upon receiving their new socks. We've designed an unpacking experience that's delightful and memorable. Gathering initial impressions enables us to understand how well we're meeting expectations. Customer reviews serve as invaluable insights driving continuous engagement and product enhancements.
In conclusion, our dedication to quality, innovation, and sustainability is woven into every stitch of our men’s cotton boat socks. From design to delivery, each stage reflects our unwavering commitment to offering nothing but the best for our customers.
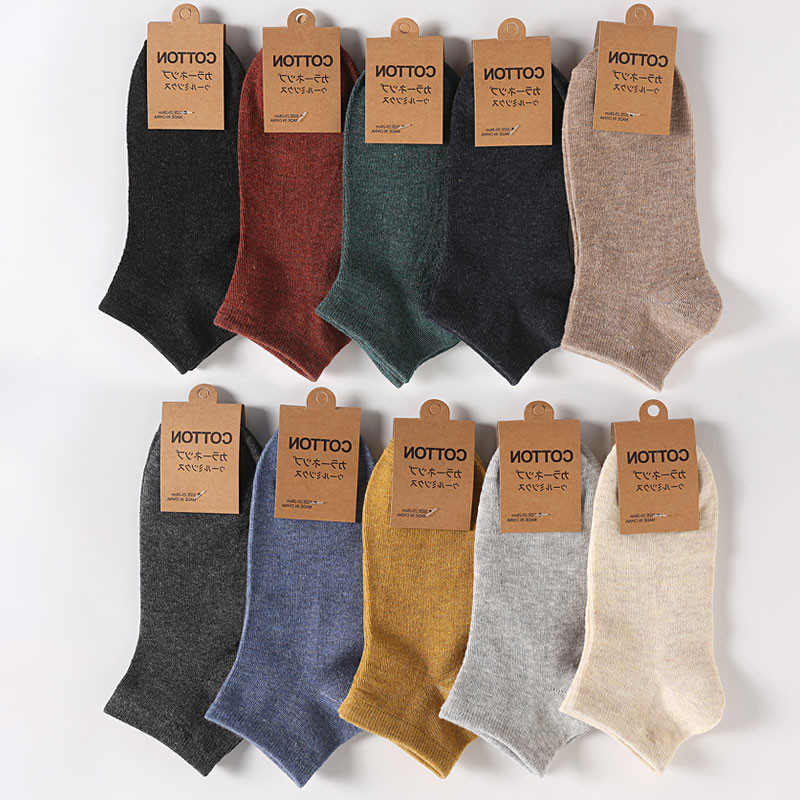